Tool Inventory
The tool inventory in a large converting plant can have a value of millions of dollars. Tracking the status of these assets is extremely important to running an effective operation. The Avista Tool Inventory application captures all usable information about the tools in your plant. Optimizing the plant investment in tooling can save a plant thousands of dollars each year not only in tooling costs but in machine downtime caused by poor tool tracking.
The system begins at the time of purchase by collecting tool cost and expected impressions as well as what items will be utilizing the tool for manufacture. When the tool physically arrives in the plant it is inspected and placed in a permanent storage location which is tracked in the application. A bar coded label may be affixed to the tool to make future tracking easier. After the initial inspection the tool status can be updated to show it is available for production. Any current orders requiring the tool can be updated to show the tooling is ready.
The system allows documents such as the print card (for printing plates), the die layout (for cutting dies), the customer PO (if there was one) and the plant PO to the supplier can be attached to the tool. These can be viewed in the office, in the tool maintenance area or at machine side for quick reference.
Each time the tool is used the system automatically updates the actual impressions for the tool directly from the machine reporting. If the plant has a standard inspection program that calls for a normal inspection before the tool is returned to storage the system will set the status to show this inspection is due and will again be updated when the inspection is complete. Major inspections can be scheduled based on total impression count.
Making sure that a tool is usable when needed and can be easily located will eliminate downtime for the machines requiring these tools.
Regardless of the plant’s tooling strategy the system will track the tool ownership and any events that occur which require the tool to leave the premises. Knowing who owns the tool, where it is if it is outside the plant will eliminate needless replacement purchases. Tool value can be amortized over its life and financial reports can be created.
This application provides a full featured management system for one of the mostly expensive areas in a converting plant.
Click to view

Easily built initial tool record
Click to view
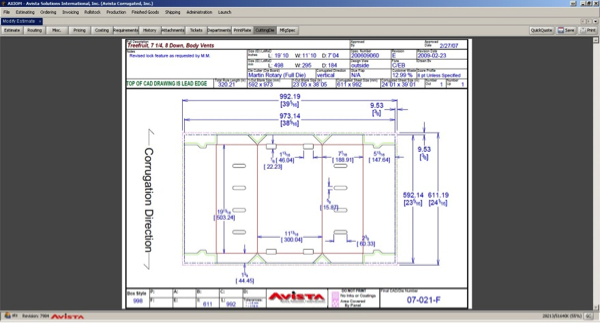
Review critical documents on line
Click to view
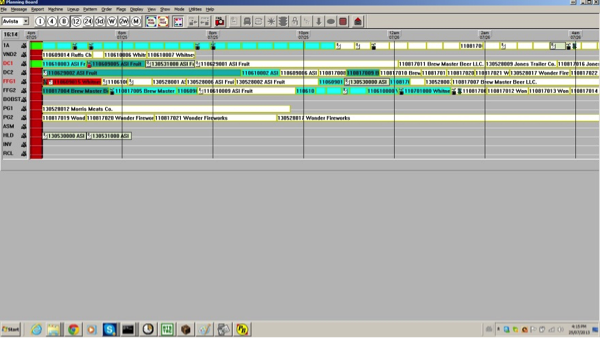
Tooling issues graphically displayed on the machine line up
Key Benefits of Tool Inventory
- Tracks the status and location of every tool in the plant
- The history of every event affecting a tool is tracked
- Tracks original cost, current value and ownership of every tool
- Tracks the supplier who made the tool as well as any supplier who performed maintenance on the tool
- Tracks the impressions for each tool and allows the creation of inspection programs
- Warns everybody when the tools required for an order are not ready and usable for an upcoming order
- Can use bar codes to simplify tool updates
- Records the disposal of tools when they are obsolete or worn out
- Can provide reports showing last usage of all tools, total usage of all tools and current value of the tool if they are amortized
Still have questions? Need more information? We should talk.
Hi, my name is Mark Gartrell with Amtech Automation and we would love to hear from you! If you're considering building a new plant, looking to improve your processes, or need to upgrade to a better solution, I hope you'll give us a call at +1 952.949.0594 to set up a time where we can connect in person or by phone, or email me directly at mgartrell@avistasoftware.com.
For information about how to contact our other employees, please visit our Contact Us page.
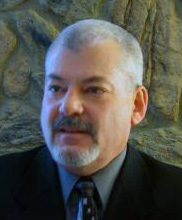
Inventory Management
WIP Inventory
When you combine the Avista Converting Set up Manager, Tag Manager, Planning Board and Shipping Manager you also...
Read MoreFinished Goods Inventory
When you combine the Avista Converting Tag Manager, Planning Board and Shipping Manager you also get advanced...
Read MoreTool Inventory
The cost of printing plates, cutting dies and other tooling in today's economy requires tight management to avoid lost...
Read More